The efficiency of wood charcoal machines is intricately linked to the type of wood feedstock utilized in the carbonization process. Understanding the relationship between wood type and charcoal machine efficiency is crucial for optimizing production outcomes and maximizing resource utilization. In this comprehensive analysis, we delve into the nuanced dynamics of this relationship, exploring the impact of wood characteristics on machine performance, product quality, and environmental sustainability.
Wood Type Diversity: Implications for Charcoal Production
The wood to charcoal machine is designed to convert various types of wood feedstock into charcoal through a process known as carbonization. The choice of wood type plays a pivotal role in determining the efficiency and effectiveness of the carbonization process. Different wood species exhibit distinct properties such as density, moisture content, lignin content, and chemical composition, which influence their suitability for charcoal production.
Density Dynamics: Balancing Porosity and Structural Integrity
Wood density, characterized by the mass of wood per unit volume, is a critical factor influencing charcoal machine efficiency. Dense woods such as oak and hickory tend to produce charcoal with higher energy content and greater stability due to their tightly packed cell structure. However, denser woods may pose challenges during carbonization, requiring higher temperatures and longer processing times to achieve optimal charcoal yields.
Conversely, less dense woods like pine and spruce are more porous and may undergo faster carbonization at lower temperatures. While these woods offer advantages in terms of process efficiency, the resulting charcoal may exhibit lower energy density and structural integrity, impacting its suitability for certain applications such as metallurgical processes or barbecue grilling.
Moisture Matters: Striking a Balance for Optimal Drying
Moisture content is another crucial factor affecting wood charcoal maker machine efficiency. Excessive moisture in wood feedstock can impede the carbonization process by requiring additional energy input to drive off moisture through evaporation. High moisture content may also lead to incomplete carbonization, resulting in lower charcoal yields and decreased product quality.
Conversely, excessively dry wood feedstock may be prone to combustion or overheating during carbonization, leading to excessive ash production and reduced charcoal yield. Therefore, achieving the optimal moisture content in wood feedstock is essential for maximizing charcoal machine efficiency and product quality.
Lignin Content: The Key to Charcoal Formation
Lignin, a complex polymer found in wood cell walls, plays a central role in the carbonization process and ultimately determines charcoal machine efficiency. During carbonization, lignin undergoes thermal degradation, breaking down into volatile compounds such as gases and tar, which are subsequently driven off, leaving behind a carbon-rich residue—the charcoal.
Woods with higher lignin content, such as hardwoods, tend to yield charcoal with greater stability and energy density due to the presence of more carbon-rich char residue. In contrast, softwoods with lower lignin content may produce charcoal with lower structural integrity and energy content, requiring additional processing steps or additives to enhance product quality.
Chemical Composition: Unlocking the Potential of Wood Species
The chemical composition of wood, including its ratio of cellulose, hemicellulose, and lignin, significantly influences charcoal machine for sale efficiency and product characteristics. Cellulose and hemicellulose are carbohydrate polymers that contribute to the formation of volatile compounds during carbonization, while lignin serves as the primary precursor for charcoal formation.
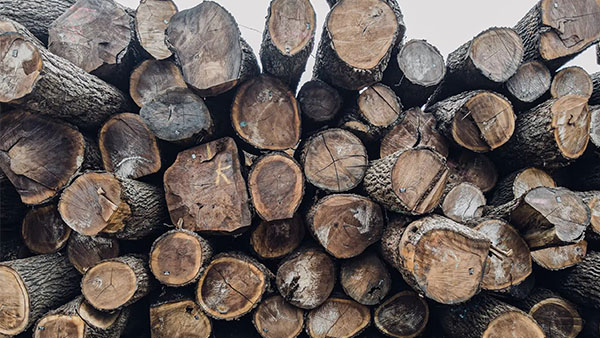
Woods with higher cellulose and hemicellulose content, such as deciduous hardwoods, tend to produce charcoal with a higher proportion of volatile compounds, which may influence combustion properties and product applications. Understanding the chemical composition of different wood species enables charcoal producers to optimize machine parameters and processing conditions to achieve desired product outcomes.
Environmental Considerations: Balancing Efficiency and Sustainability
While maximizing charcoal machine efficiency is essential for economic viability, it is equally important to consider the environmental implications of wood type selection and carbonization processes. Sustainable wood sourcing practices, including forest management, reforestation efforts, and utilization of waste wood residues, play a critical role in mitigating deforestation and preserving biodiversity.
Additionally, adopting energy-efficient carbonization technologies and implementing emissions control measures can reduce the environmental footprint of charcoal production, minimizing air pollution and greenhouse gas emissions. By prioritizing both efficiency and sustainability, charcoal producers can achieve a balance that promotes long-term environmental stewardship and economic prosperity. Consult Beston China for more information.
Conclusion: Harnessing the Potential of Wood Charcoal Machines
In conclusion, the relationship between wood type and charcoal machine efficiency is multifaceted, with wood characteristics influencing process parameters, product quality, and environmental sustainability. By understanding the diverse properties of different wood species and their implications for carbonization, charcoal producers can optimize machine performance, enhance product quality, and minimize environmental impact.
Moving forward, ongoing research and technological innovation in wood charcoal machine design, process optimization, and sustainable wood sourcing practices will continue to drive advancements in the field. By harnessing the potential of wood charcoal machines and prioritizing efficiency, quality, and sustainability, the charcoal industry can play a vital role in addressing global challenges such as waste management, energy security, and climate change mitigation.